The Role of Infrared Sensors in Light Detection and Ranging - LiDAR
What is LiDAR?
LiDAR (Light Detection and Ranging) is a system for measuring distance and mapping objects and environments. A LiDAR system emits thousands to millions of laser pulses per second and captures the reflected infrared light with a sensor. The process creates a detailed 3D map of the area covered. This ‘point cloud’ as it’s known, represents the surface characteristics of the scanned environment.
LiDAR can be used for:
- Autonomous and assisted driving vehicle navigation, where it provides detailed and dynamic 3D data about the vehicle's surroundings.
- Creating high-resolution maps of the Earth's surface, including vegetation, buildings, and other features.
- Environmental monitoring and management, such as assessing forest biomass and erosion patterns.
- Archaeological and historical site documentation by mapping structures and landscapes in 3D.
The performance of a LiDAR system is dependent upon these key factors:
- The power level and pulse settings of the laser diode that creates the pulses
- The sensitivity of the infrared sensor that detects the reflected signals
- The type and quality of mechanical and optical components used in the system
- The performance of the electronic processing circuits and information displays
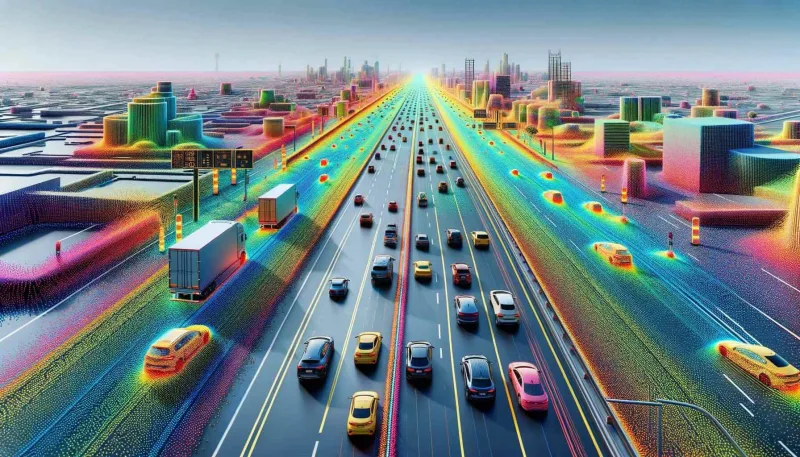
Most LiDAR systems use a technique called time of flight to build a 3D map of their surroundings. Using precise timing information, the LiDAR system knows the time of flight between the emission of a laser pulse and its reception. From this, it calculates the distance to the object from which a reflection occurred. The LIDAR system also knows the angle of the pulse in the horizontal and vertical plane and the distance to the object, from which it builds a 3D picture from spherical coordinates. This means every point measured will have its 3D position known with respect to the LiDAR coordinate frame, its time of recording, and the intensity of the reflected beam. This allows LiDAR to map its immediate environment. The more laser pulses that are sent out each second, the higher the point cloud density and the better the 3D map.
What sensors are used in LiDAR?
LiDAR operates in the infrared spectrum. The infrared sensors used in LiDAR are typically either a Silicon Photomultiplier (SiPM) for systems operating in the infrared spectrum at a wavelength of 905 nm or an avalanche photodiode (APD) for systems operating at 1550 nm. APDs are a type of detector that exhibits internal amplification when a reverse-biased voltage is applied. The optimal level of sensitivity is achieved when the noise of the APD matches that of the following amplifier. When infrared light hits an APD, an electrical current is generated that flows through the device. The photocurrent is amplified and detected to yield the timing information. The chemical composition of the device determines its responsivity to various infrared wavelengths as shown in the diagram.
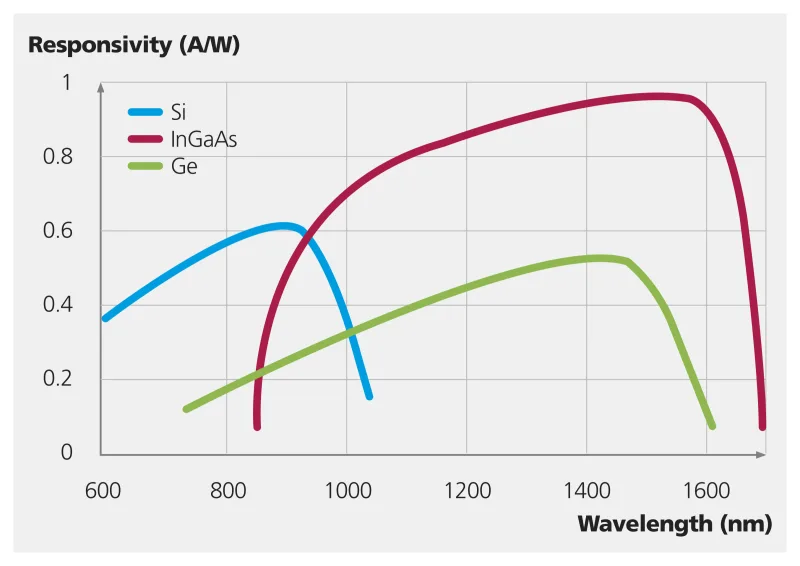
Silicon diodes have a peak response at about 905 nm and indium gallium arsenide (InGaAs) diodes at around 1,550 nm. As a result, these are the two most common wavelengths used in LiDAR systems. Germanium diodes can be used but they are less sensitive than InGaAs parts and their sensitivity peaks at a slightly shorter wavelength than InGaAs.
Why LiDAR wavelength matters
905 nm systems benefit from the availability of lower-cost, silicon-based sensors that deliver high sensitivity. However, because this wavelength is close to that of visible light, sunlight and other ambient light sources, can cause interference and add noise. For the same reason, 905 nm systems raise eye safety concerns, limiting the amount of laser power that can be emitted from a 905 laser Many lower power lasers are therefore typically used in a 905 LIDAR system to achieve reliable performance over more than a few tens of metres.
The 1,550 nm wavelength is far enough from the visible spectrum to allow far more powerful lasers to be used. These lasers can operate with much higher power while remaining eye-safe to the Class 1 standard. The 1550 nm spectrum therefore provides much greater design freedom as fewer lasers and smaller optical apertures can be used in the LiDAR system. Combined with a greater ability to penetrate fog, haze, and dust, this makes the longer wavelength suitable for front-facing LiDAR systems that need to detect potential obstructions over 100 metres from a vehicle, which is a key requirement for automated driving at speed.
The availability of higher laser power also makes it easier for sensors to detect light reflected from objects that have high absorbance, such as tyres on the road. Detecting the objects in a way that allows assisted driving systems the time to react requires high sensitivity in the sensor array so that the smallest of signals can be detected.
How a performance breakthrough in 1,550 nm IR sensors addresses the challenges
Phlux’s Aura family of 1,550 nm IR sensors, launched in April 2024, are based on the company’s Noiseless InGaAs® APD technology. The devices are 12X more sensitive than traditional best-in-class InGaAs APDs, so they can extend the operating range of LiDAR by up to 50% because they can detect low-level signals above ambient noise.
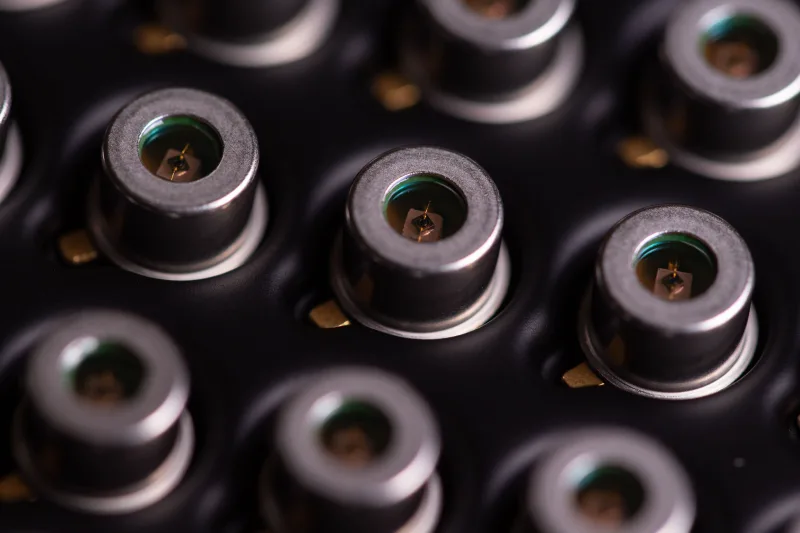
In new designs, these sensors enable up to 12X greater image resolution for a given laser power in a 1,550 nm LiDAR system. There are also potential reductions in LiDAR system size and cost because lower-power lasers with smaller optical apertures can be used without impacting performance. A further benefit is that the new APDs operate at up to +85 °C without performance degradation, which is a significantly higher temperature than traditional parts, so thermal management is simplified.
In existing designs, the new APDs are drop-in replacements for existing parts, so some of the benefits described above can be achieved quickly and easily.
You can read more about the underlying technology here and product data is available here.